- 1,603
- IN
- Eric_J2358
In recent years sanctioning bodies such as Grand-Am - IndyCar and Formula One (optional) use a Variable Ratio Steering system.
some of these systems are powered but not in the conventional sense.
as of yet no one even bothers to measure the force required to turn the wheel at the rim.
although the force required is slightly higher on road course tracks as opposed to oval the total is much lower than it was twenty years ago.
you do not want a driver to put up with 40lbs at the rim for two hours of racing. he would end up in the pitts within twenty lapps suffering from fatigue.
as of 2008 IndyCar steering systems have changed and by good buddy (Les Mactaggart)
has mentioned to me that the force required is around 13lbs on road courses with as low as 9lbs on ovals. in my experience in racing it seems to vary from 10 to 16 lbs in recent years.
in racing you need to be able to respond quickly with steering input and having to fight the wheel would be of no help. we need a light steering with good feedback from the system.
Yeah I also found that one:
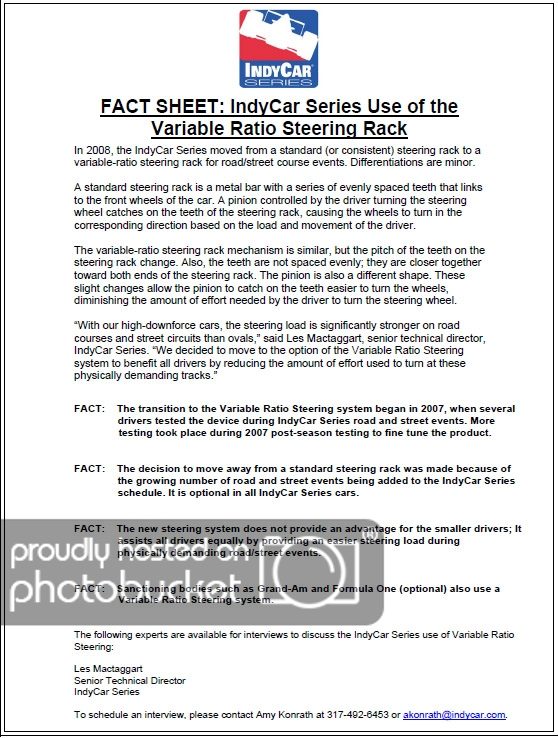
I didn't post it before since it didn't really have any specific info.